Vaporizing plastics recycles them into nothing but gas
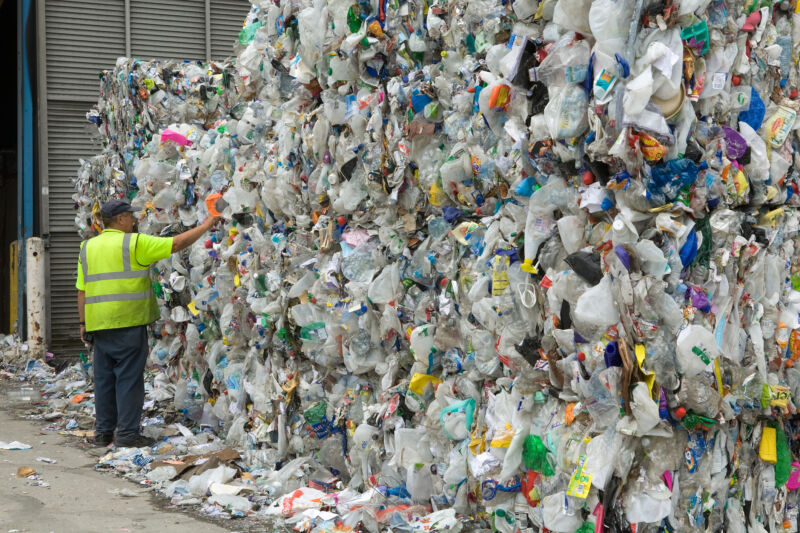
Our planet is choking on plastics. Some of the worst offenders, which can take decades to degrade in landfills, are polypropylene—which is used for things such as food packaging and bumpers—and polyethylene, found in plastic bags, bottles, toys, and even mulch.
Polypropylene and polyethylene can be recycled, but the process can be difficult and often produces large quantities of the greenhouse gas methane. They are both polyolefins, which are the products of polymerizing ethylene and propylene, raw materials that are mainly derived from fossil fuels. The bonds of polyolefins are also notoriously hard to break.
Now, researchers at the University of California, Berkeley have come up with a method of recycling these polymers that uses catalysts that easily break their bonds, converting them into propylene and isobutylene, which are gasses at room temperature. Those gasses can then be recycled into new plastics.
“Because polypropylene and polyethylene are among the most difficult and expensive plastics to separate from each other in a mixed waste stream, it is crucial that [a recycling] process apply to both polyolefins,” the research team said in a study recently published in Science.
Breaking it down
The recycling process the team used is known as isomerizing ethenolysis, which relies on a catalyst to break down olefin polymer chains into their small molecules. Polyethylene and polypropylene bonds are highly resistant to chemical reactions because both of these polyolefins have long chains of single carbon-carbon bonds. Most polymers have at least one carbon-carbon double bond, which is much easier to break.
While isomerizing ethenolysis had been tried by the same researchers before, the previous catalysts were expensive metals that did not remain pure long enough to convert all of the plastic into gas. Using sodium on alumina followed by tungsten oxide on silica proved much more economical and effective, even though the high temperatures required for the reaction added a bit to the cost
In both plastics, exposure to sodium on alumina broke each polymer chain into shorter polymer chains and created breakable carbon-carbon double bonds at the ends. The chains continued to break over and over. Both then underwent a second process known as olefin metathesis. They were exposed to a stream of ethylene gas flowing into a reaction chamber while being introduced to tungsten oxide on silica, which resulted in the breakage of the carbon-carbon bonds.
The reaction breaks all the carbon-carbon bonds in polyethylene and polypropylene, with the carbon atoms released during the breaking of these bonds ending up attached to molecules of ethylene.“The ethylene is critical to this reaction, as it is a co-reactant,” researcher R.J. Conk, one of the authors of the study, told Ars Technica. “The broken links then react with ethylene, which removes the links from the chain. Without ethylene, the reaction cannot occur.”
The entire chain is catalyzed until polyethylene is fully converted to propylene, and polypropylene is converted to a mixture of propylene and isobutylene.
This method has high selectivity—meaning it produces a large amount of the desired product. That means propylene derived from polyethylene, and both propylene and isobutylene derived from polypropylene. Both of these chemicals are in high demand, since propylene is an important raw material for the chemical industry, while isobutylene is a frequently used monomer in many different polymers, including synthetic rubber and a gasoline additive.
Mixing it up
Because plastics are often mixed at recycling centers, the researchers wanted to see what would happen if polypropylene and polyethylene underwent isomerizing ethenolysis together. The reaction was successful, converting the mixture into propylene and isobutylene, with slightly more propylene than isobutylene.
Mixtures also typically include contaminants in the form of additional plastics. So the team also wanted to see whether the reaction would still work if there were contaminants. So they experimented with plastic objects that would otherwise be thrown away, including a centrifuge and a bread bag, both of which contained traces of other polymers besides polypropylene and polyethylene. The reaction yielded only slightly less propylene and isobutylene than it did with unadulterated versions of the polyolefins.
Another test involved introducing different plastics, such as PET and PVC, to polypropylene and polyethylene to see if that would make a difference. These did lower the yield significantly. If this approach is going to be successful, then all but the slightest traces of contaminants will have to be removed from polypropylene and polyethylene products before they are recycled.
While this recycling method sounds like it could prevent tons upon tons of waste, it will need to be scaled up enormously for this to happen. When the research team increased the scale of the experiment, it produced the same yield, which looks promising for the future. Still, we’ll need to build considerable infrastructure before this could make a dent in our plastic waste.
“We hope that the work described…will lead to practical methods for…[producing] new polymers,” the researchers said in the same study. “By doing so, the demand for production of these essential commodity chemicals starting from fossil carbon sources and the associated greenhouse gas emissions could be greatly reduced.”
Science, 2024. DOI: 10.1126/science.adq731
Vaporizing plastics recycles them into nothing but gas Read More »