Silicon plus perovskite solar reaches 34 percent efficiency
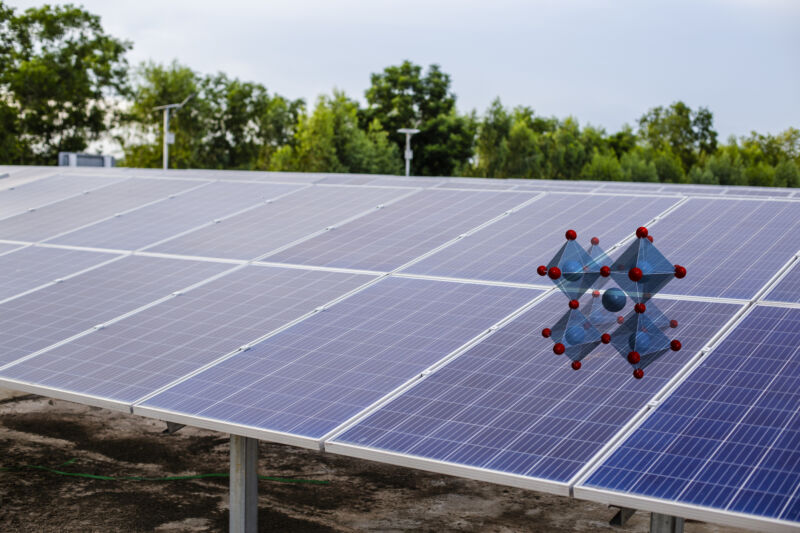
Enlarge / Some solar panels, along with a diagram of a perovskite’s crystal structure.
As the price of silicon panels has continued to come down, we’ve reached the point where they’re a small and shrinking cost of building a solar farm. That means that it might be worth spending more to get a panel that converts more of the incoming sunlight to electricity, since it allows you to get more out of the price paid to get each panel installed. But silicon panels are already pushing up against physical limits on efficiency. Which means our best chance for a major boost in panel efficiency may be to combine silicon with an additional photovoltaic material.
Right now, most of the focus is on pairing silicon with a class of materials called perovskites. Perovskite crystals can be layered on top of silicon, creating a panel with two materials that absorb different areas of the spectrum—plus, perovskites can be made from relatively cheap raw materials. Unfortunately, it has been difficult to make perovskites that are both high-efficiency and last for the decades that the silicon portion will.
Lots of labs are attempting to change that, though. And two of them reported some progress this week, including a perovskite/silicon system that achieved 34 percent efficiency.
Boosting perovskite stability
Perovskites are an entire class of materials that all form the same crystal structure. So, there is plenty of flexibility when it comes to the raw materials being used. Perovskite-based photovoltaics are typically formed by what’s called solution processing, in which all the raw materials are dissolved in a liquid that’s then layered on top of the panel-to-be, allowing perovskite crystals to form across its entire surface. Which is great, except that this process tends to form multiple crystals with different orientations on a single surface, decreasing performance.
Adding to the problems, perovskites are also not especially stable. They’re usually made of a combination of positively and negatively charged ions, and these have to be present in the right ratios to form a perovskite. However, some of these individual ions can diffuse over time, disrupting the crystal structure. Harvesting solar energy, which involves the material absorbing lots of energy, makes matters worse by heating the material, which increases the rate of diffusion.
Combined, these factors sap the efficiency of perovskite solar cells and mean that none lasts nearly as long as a sheet of silicon. The new works tackle these issues from two very different directions.
The first of the new papers tackles stability by using the flexibility of perovskites to incorporate various ions. The researchers started by using a technique called density functional theory to model how different molecules would behave when placed into a spot normally occupied by a positively charged ion. And the modeling got them excited about a molecule called tetrahydrotriazinium, which has a six-atom ring composed of alternating carbon and nitrogen atoms. The regular placement of nitrogens around the ring allows it to form regular interactions with neighboring atoms in the crystal structure.
Tetrahydrotriazinium has a neutral charge when only two of the nitrogens have hydrogens attached to them. But it typically grabs a charged hydrogen (effectively, a proton) out of solution, giving it a net positive charge. This leaves each of its three nitrogens associated with a hydrogen and allows the positive charge to be distributed among them. That makes this interaction incredibly strong, meaning that the hydrogens are extremely unlikely to drift off, which also stabilizes the crystal structure.
So, this should make perovskites much, much more stable. The only problem? Tetrahydrotriazinium tends to react with lots of other chemicals, so it’s difficult to provide as a raw material for the perovskite-forming solution.
Silicon plus perovskite solar reaches 34 percent efficiency Read More »